Understanding Injection Mold Plastic: A Comprehensive Overview
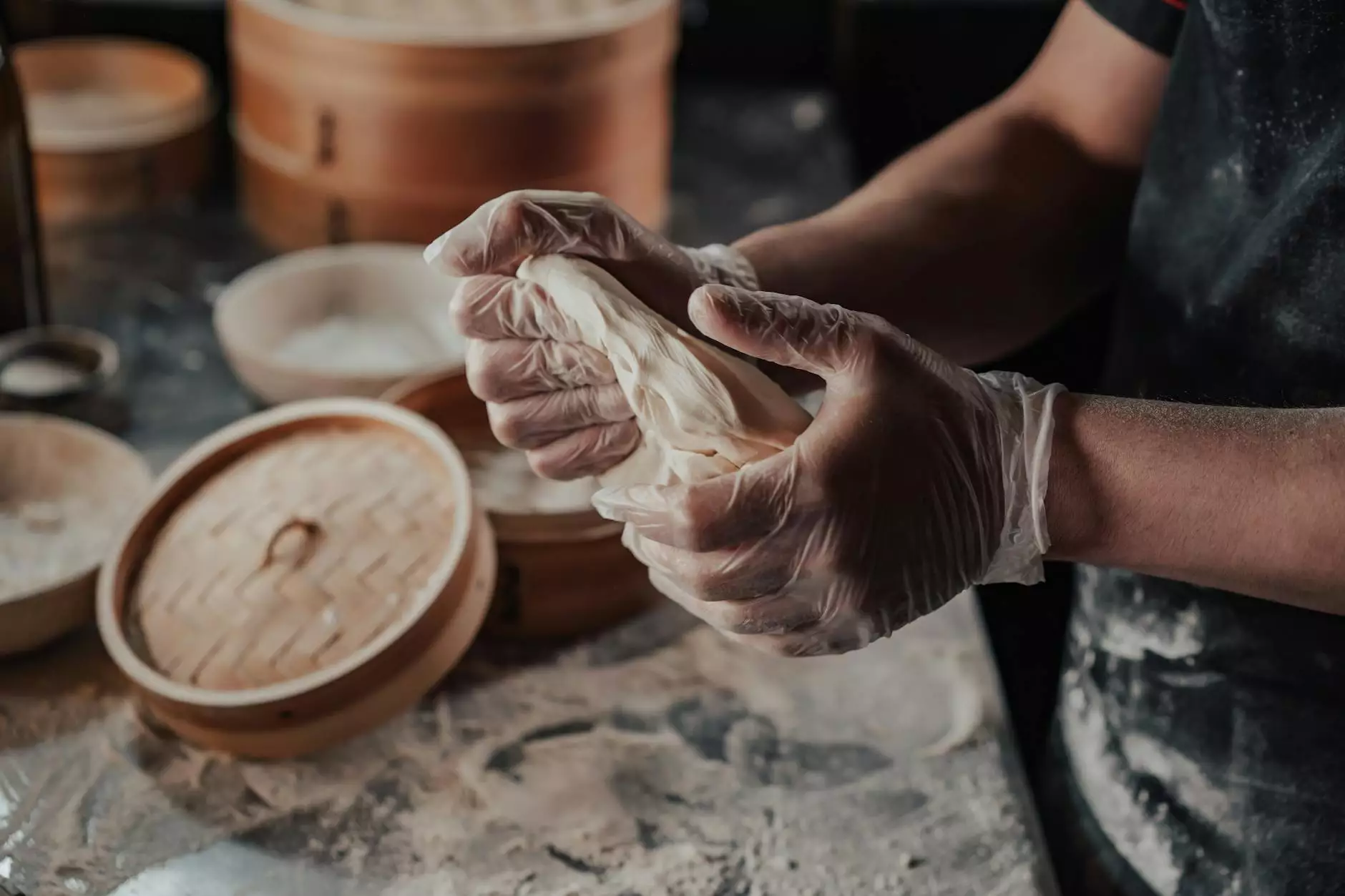
In the dynamic realm of manufacturing, injection mold plastic plays a pivotal role in producing high-quality, durable products. This innovative technique revolutionizes the way plastic items are created, ensuring efficiency, precision, and versatility. Whether in automotive parts, consumer goods, or electronic enclosures, the significance of injection molding cannot be overstated.
What is Injection Molding?
Injection molding is a manufacturing process that involves injecting molten plastic into a mold to create various products. This method is particularly favored for its ability to mass-produce complex shapes and intricate designs with uniform quality. The process typically includes:
- Clamping: The mold is securely closed under pressure.
- Injection: Molten plastic is injected into the mold at high speed.
- Cooling: The plastic is allowed to cool and solidify.
- Ejection: The finished product is ejected from the mold.
The Importance of Injection Mold Plastic in Modern Manufacturing
The demand for injection mold plastic is surging, thanks to its numerous advantages:
- Cost-Effectiveness: High-volume production reduces the per-unit cost significantly.
- Precision: The molds can produce parts with high accuracy and tight tolerances.
- Flexibility: Various types of plastics can be used, allowing for customization.
- Durability: Items produced via this method are often more robust compared to alternatives.
Types of Plastics Used in Injection Molding
The selection of the right type of plastic is crucial for the success of the injection molding process. Some common materials include:
- Polyethylene (PE): Known for its flexibility and toughness, suitable for various applications.
- Polypropylene (PP): Offers high chemical resistance and is often used for containers and automotive parts.
- Polyvinyl Chloride (PVC): Durable and cost-effective, commonly used in flooring and plumbing products.
- ABS (Acrylonitrile Butadiene Styrene): Known for its strength and impact resistance, ideal for consumer electronics.
Steps in the Injection Molding Process
1. Designing the Mold
The first step in injection molding is to design the mold. This involves using Computer-Aided Design (CAD) software to create an accurate mold specification that will meet the product requirements in terms of functionality and aesthetic appeal.
2. Creating the Mold
Once the design is finalized, the mold is produced using high-precision machinery. This step requires careful attention to detail to ensure that the mold can withstand the pressure of injection and produce high-quality parts.
3. Melting the Plastic
The plastic pellets are heated to a melting point in a heated barrel, transforming them into a molten state that can flow easily into the mold.
4. Injecting the Plastic
The molten plastic is injected into the mold through a nozzle under high pressure. This ensures that the material fills every cavity of the mold, creating a part that's ready for use.
5. Cooling and Solidification
After injection, the mold is cooled. This step is essential to harden the plastic and ensure it keeps the shape formed in the mold.
6. Ejecting the Finished Part
Once cooled, the mold opens, and ejector pins remove the finished plastic part. At this stage, the part may require secondary operations such as trimming or surface finishing.
Applications of Injection Mold Plastic
The versatility of injection mold plastic allows for its utilization across various industries:
- Automotive Industry: Manufacturing of dashboards, interior trims, bumpers, and other critical components.
- Consumer Products: Production of toys, kitchenware, and household appliances.
- Medical Devices: Creation of syringes, inhalers, and various other medical instruments which require high precision and hygiene.
- Electronics: Enclosures for electronic devices and components that need to be lightweight yet durable.
Advantages of Using Injection Mold Plastic
Here are some additional benefits of choosing injection molding for plastic manufacturing:
- Reduced Waste: The precision of the molding process minimizes excess material.
- High Production Rates: Once the mold is created, hundreds or thousands of parts can be produced in a short time.
- Consistent Quality: The automated nature of the process ensures uniformity across large batches.
- Complex Geometries: Injection molding allows for the creation of intricate designs that would be difficult or impossible to achieve with other manufacturing methods.
The Future of Injection Mold Plastic
As technology advances, the future of injection mold plastic looks promising. Innovations in materials, such as bio-based plastics and reinforced composites, are being developed to meet the growing demand for sustainable solutions. Moreover, the integration of Industry 4.0 principles, including automation and data analytics, is poised to enhance efficiency and flexibility in the injection molding process.
Choosing the Right Injection Mold Manufacturer
Partnering with a reliable injection mold manufacturer is crucial for achieving quality results. When selecting a manufacturer, consider the following:
- Experience: Look for a company with a proven track record in the industry.
- Customization Options: Ensure they can design and produce molds that meet your specific requirements.
- Quality Assurance: Choose a manufacturer that adheres to high-quality standards and has a robust process for quality control.
- Customer Service: A supportive and responsive team can make the process smoother and more efficient.
Conclusion
In conclusion, injection mold plastic has transformed the manufacturing landscape, enabling the production of a myriad of products with unmatched precision and efficiency. From automobiles to consumer goods, the applications are extensive and vital. As industries continue to evolve, so too will the techniques and materials used in injection molding, offering even greater possibilities for manufacturers looking to innovate and improve their product offerings. Embracing this technology can lead to greater cost savings, increased product quality, and a more sustainable manufacturing process. As we look to the future, injection molding will remain at the forefront of manufacturing technology.